Thursday 17 Feb.
Excitement(?) had been mounting for Pete’s Epoxy Workshop. I had got tea and home baked Anzac biscuits organised thanks to my wife. The doors opened at 9.45 and Kay had already set up an urn and mugs for tea. In walked a pleasing crowd of people past the desk with the Covid signs and Paul H, who was press-ganged into being the Covid officer checking vaccination status. We were all a bit unsure of the mask wearing protocol particularly as both ends of the shed are open and enjoy a good through breeze. Let’s just say its a personal choice but the advice from us is to keep them on.
John B and Nick S had brought rock cakes and fruit bread respectively, so there was more than enough to go around the 15 attendees (16 if you count John S’s dog) .
Pete was keen to get underway and started his workshop as all good workshops do, with health and safety tips as epoxy is not something you want to get on your skin or worse places. Nitrile gloves (re-useable if you leave the epoxy to dry on them), long sleeved shirts, eye protection, lots of fresh air or carbon filter masks (not cloth masks which concentrate the fumes). Most people don’t have a problem with epoxy fumes but if you work with it really regularly you can become allergic to it.
Next it was onto making scarfing joint surfaces. This was something that a number of us found a fairly daunting prospect but Pete made it look relatively straight forward. After lining up 4 pieces of plywood on the bench set the requisite 60mm back from the planned pointy scarph edge of the underlying plank, he planed away the top corners until there was a single slope down to the bottom edge on the end of the bench. The plywood laminates acted like contour lines guiding the accuracy and flatness of the slope.
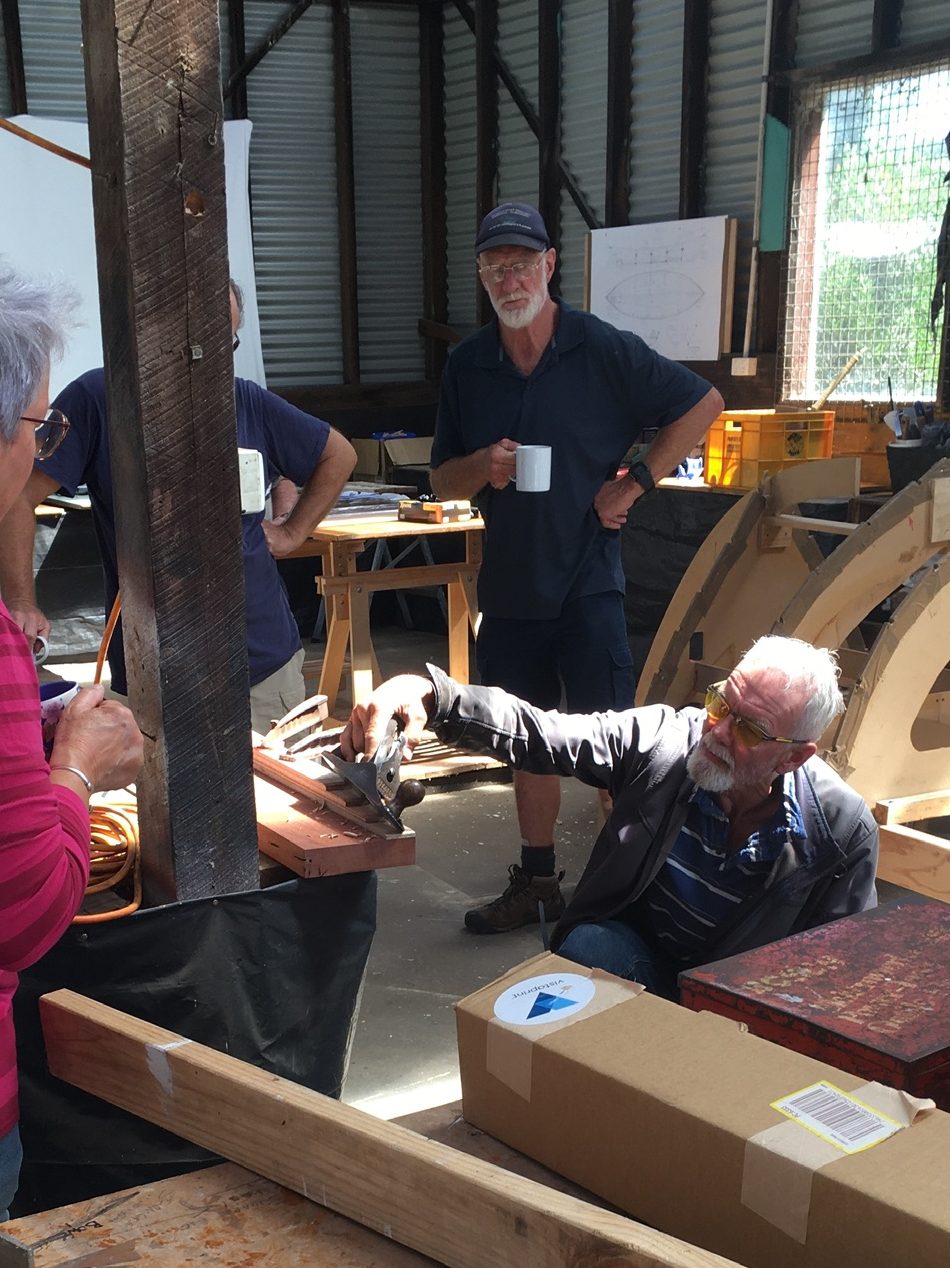
A timely tea break was had after the realisation that there had been a mis-communication over who was supplying the epoxy (ours hadn’t arrived yet). Pete did a dash back to his shed for supplies while we introduced ourselves to our fellow wannabe boat builders and the dog ignored us all.
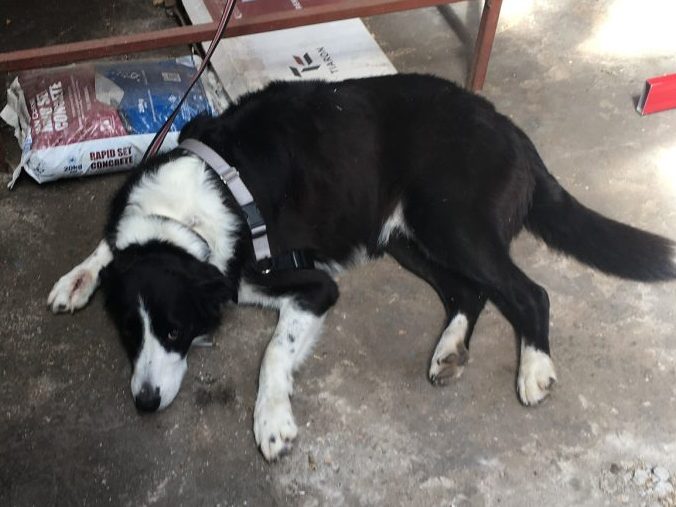
Back to work and Pete told us all about epoxy’s temperature dependence and how the warmth of your hands or vigorous stirring can heat it up and make it go off quicker. It is also an exothermic reaction so that large amounts generate their own heat and can smoulder or burst into flames so mix 5 small amounts rather than 1 big bucket full. He was demonstrating with West Systems that has microfibre filler additives that thicken up the resin to make a strong glue that’s tuff to sand or a fairing compound to fill divots to be sanded later.
Mixing the resin and hardener in the pumped proportions required is, Pete tells us, a Zen moment requiring slow steady and thorough stirring like raking pebbles in a Japanese garden. I hadn’t considered Zen coming into it, but perhaps there is a book in this “Zen and the art of St Ayles Skiff building”.
Liberally apply the resin to the surfaces that you intend to join and watch it sink in, especially on the end grains, then putty up those surfaces with epoxy mixed to the consistency of smooth peanut butter. Push the surfaces together and watch it squeeze out but always leave 05.-1mm of glue in the join for it not to end up glue starved. Clean up the excess while its wet because what you leave behind will require much tougher measures (heavy machinery or even explosives!) to remove it tomorrow.

Pete talked us through glueing scarph joints, end to end joints, and butt joints. The latter made with a home made filleting tool in the form of a diagonally cut piece of PVC pipe.
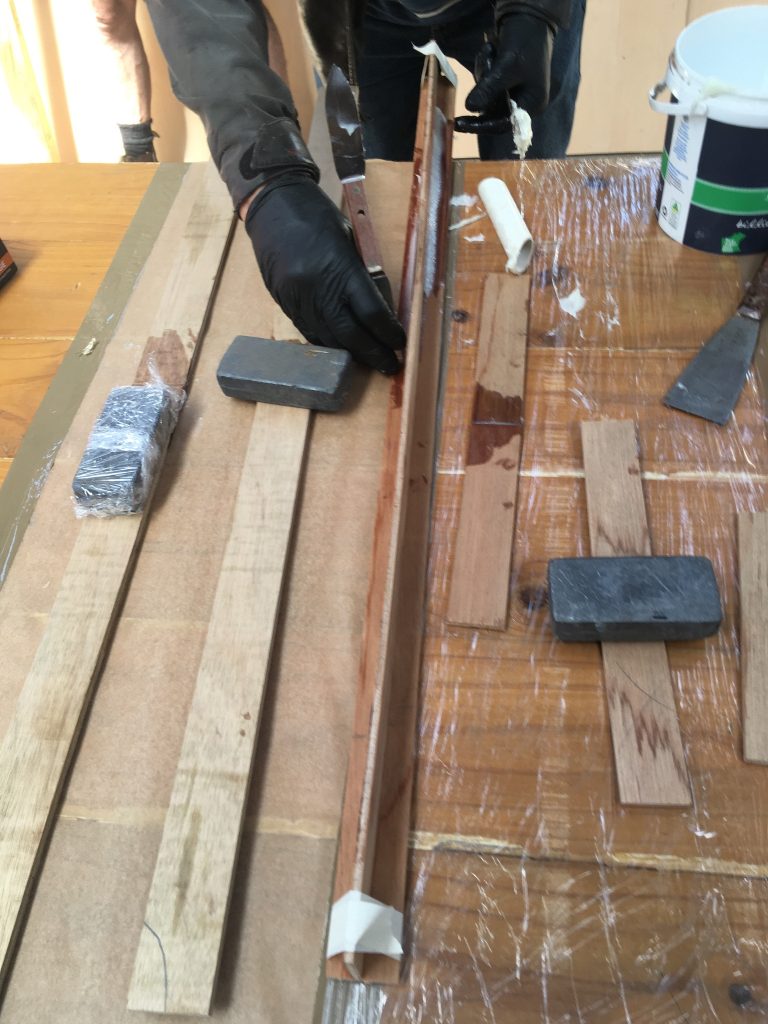
You’ll note the table has various coverings including baking paper, cling wrap, packing tape and (not shown) thick plastic of a dog food bag. I did this as a sort of scientific experiment to see which has the least adherent properties when it comes to dry epoxy glue. We’ll see the results on Monday.
Pete wrapped up his course with a demonstration of how to clean up all the tools and the mixing container with white vinegar ready for reuse. This trick I had learnt from him some years ago and it always amazes me how efficient it is and how few people know about it.
I thanked Pete and we all agreed it had been a great workshop and had allayed a lot of fears in dealing with epoxy glue. I’m sure we’ll all be experts by the time we have finished glueing 2 skiff kits together.
Surprisingly there were still cakes left but I scarphed a couple, or something like that, while I cleaned up and made sure Harry, who had attended, was comfortable with the shed’s rearrangement. Kay came across with two cucumbers for me from her garden which was brilliant. Thanks Kay.
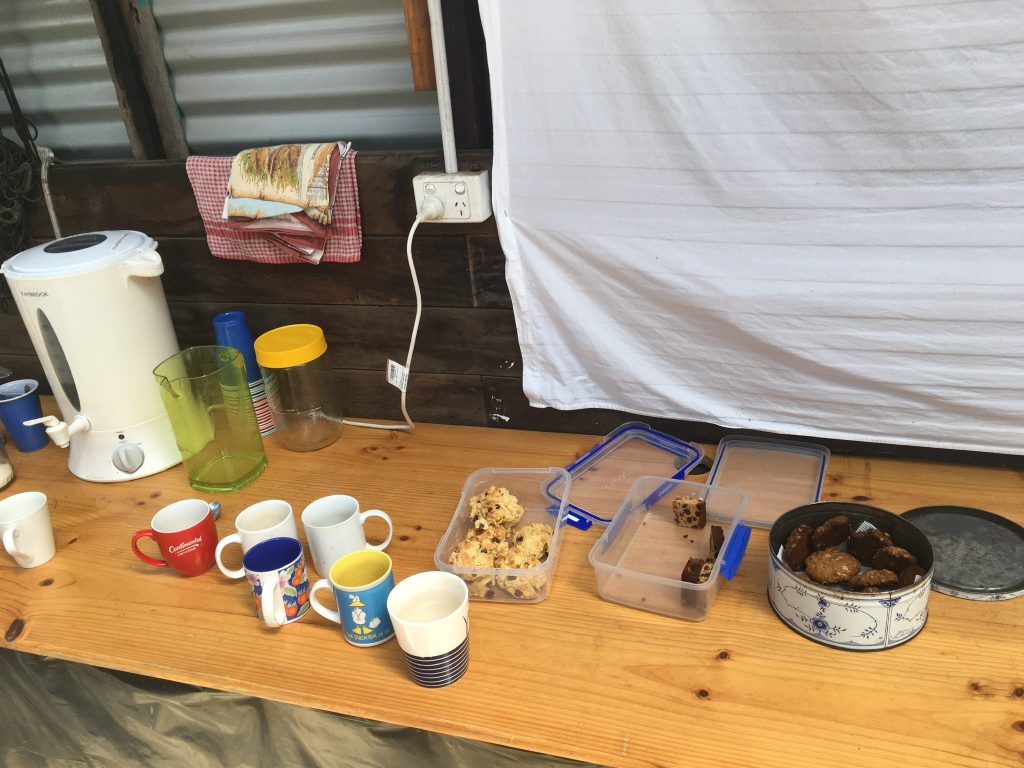
We’ll be back in the shed on Monday at 9am, making more preparations for the kit arrivals. On Tuesday we will have our first visitation of the Denmark Senior High School year 11 boat building students to give us a hand to laser level the building frame and fix it in place.
Thanks again Pete Wilson of Hand Hewn, bespoke carpentry and timber supplies.
Apologies for the length of this missive. Cheers Dave